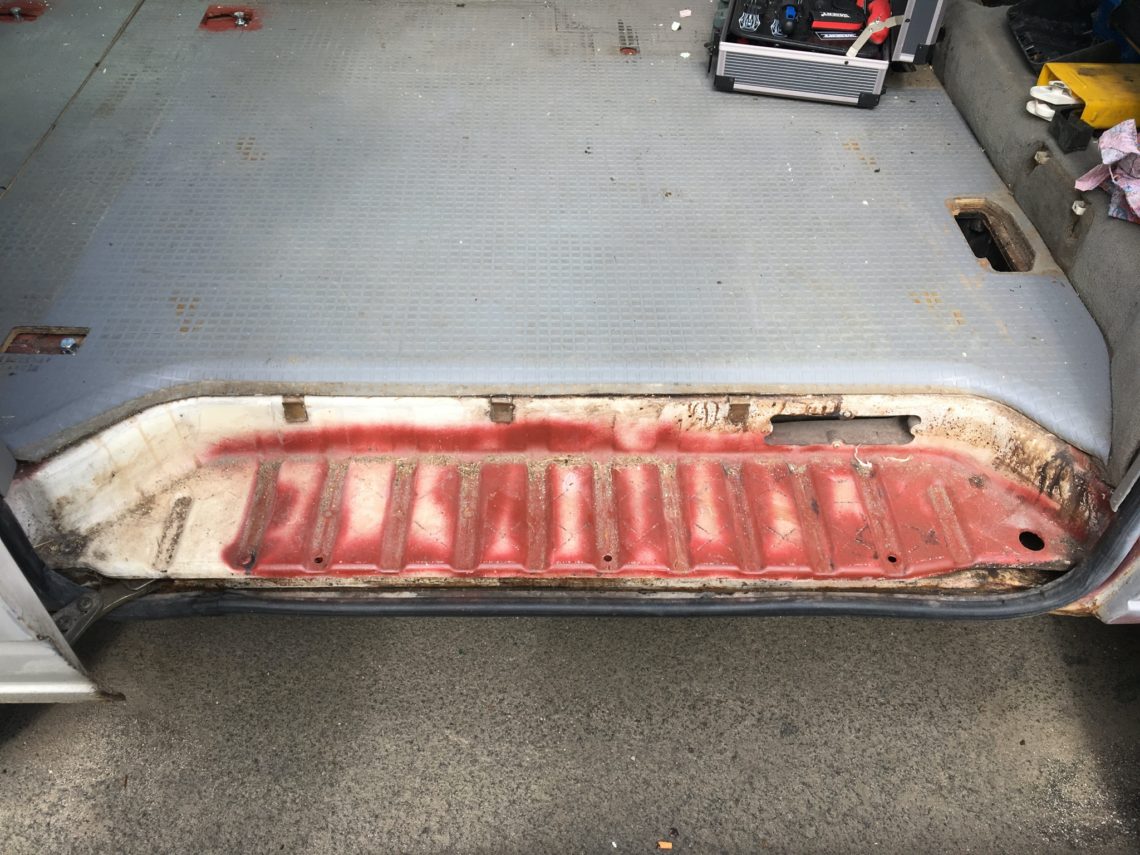
Busausbau: Die Bodenplatte
Bei der „Alles muss raus“-Aktion bei unserem VW-Bus wurde schnell klar, dass wir die Bodenplatte austauschen wollen. Die alte sah einfach nicht mehr gut aus und wenn sowieso schon einmal alles draußen ist, bietet es sich an, diese gleich auszutauschen.
Doch warum braucht es überhaupt eine Bodenplatte? Einfach gesagt: Die Platte gleicht Unebenheiten aus, schützt die Karosserie von oben und man kann Einbauten leichter daran befestigen. Hinzu kommt die zusätzliche Dämmung von unten, erst Recht, wenn man unter der Bodenplatte noch Armaflex verlegt. Auf der ebenen Fläche einer Bodenplatte lässt sich leichter ein wohnlicher Fußboden verlegen, der sich viel leichter reinigen lässt als der Blechboden.
Zuerst kommt die alte, leicht gammelige Platte raus und der Innenraum wird das erste Mal gereinigt. Nun folgen grobe Arbeiten mit der Flex: Auf dem Bodenblech sitzen metallene Platten drauf. Wir vermuten, sie dienten zur Befestigung von zusätzlichen Sitzen. Die wollen wir entfernen. Also ran mit der Flex, die Funken sprühen.
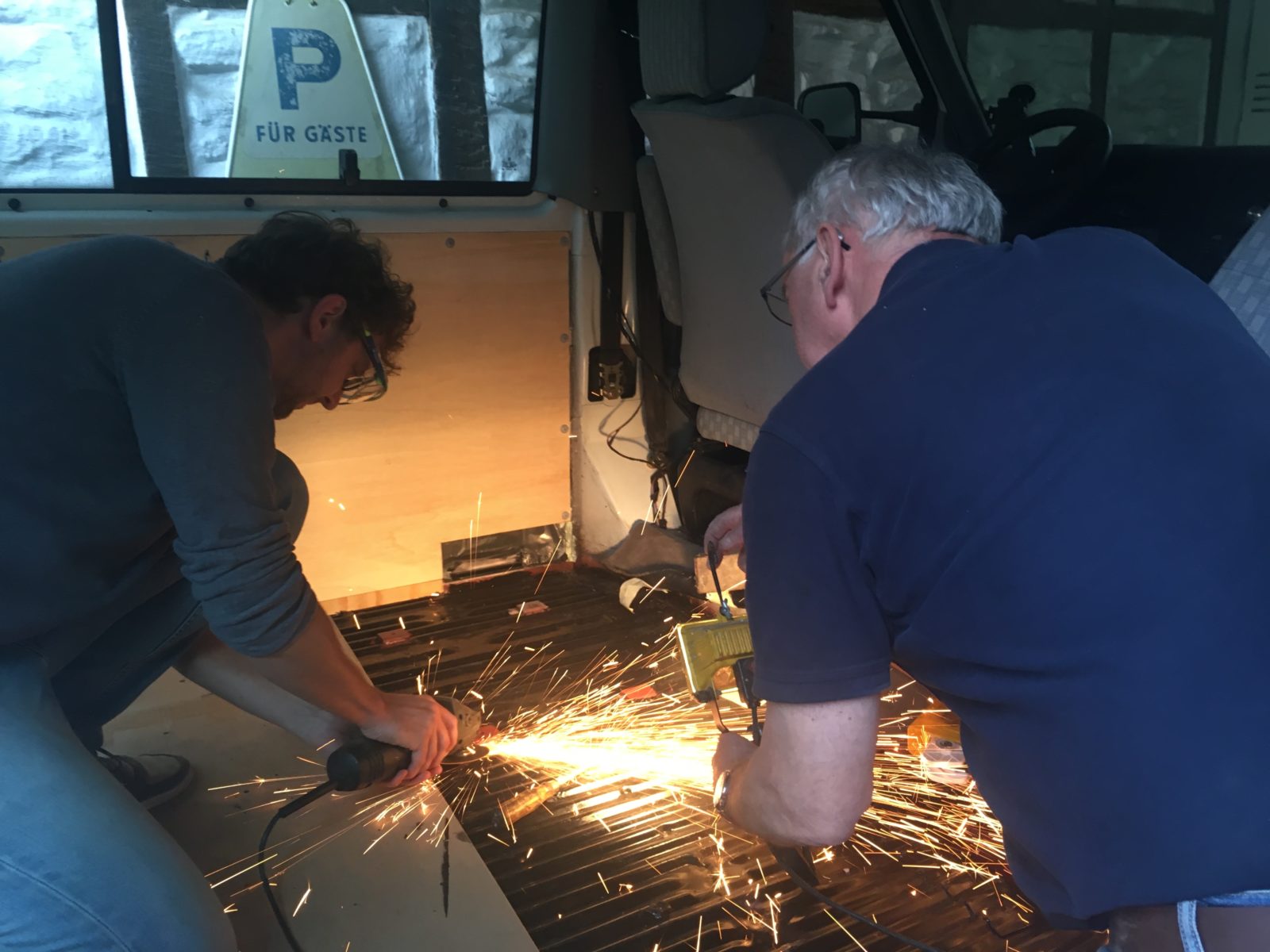
Da wir bereits mit den groben Arbeiten beschäftigt sind, setzen wir die Löcher zur Befestigung der Bodenplatte sowie für die hintere Sitzbank (wie wir die hintere Sitzbank befestigt haben, erkläre wir in einem eigenen Beitrag). Das passiert zunächst mit der Bohrmaschine. In die Löcher kommen Nietmuttern. In denen ziehen sich später die Schrauben fest.
Werbung
Die Muttern werden mit einer Spezialzange eingepresst. Dazu für die Lochgröße unbedingt die Angaben der Nietmutternhersteller beachten, sonst wackeln nachher die Muttern im Blech. Wir haben Schrauben mit einem Durchmesser von 8mm verwendet, an manchen Stellen aber auch 6mm-Schrauben. Gebohrt haben wir mit einem 10,5 mm-Bohrer. Die 6mm-Schrauben lassen sich mit einer Nietmutternzange leichter quetschen und heben auch in der Bodenplatte.
Empfehlen können wir, vorher unbedingt auf einem Probeblech und mit unterschiedlichen Löchern zu testen (z.B. 10mm, 10,2mm, 10,5mm, 11mm). Bei dünnem Blech fransen die Löcher gerne aus – auch dann wackeln wieder die Muttern.
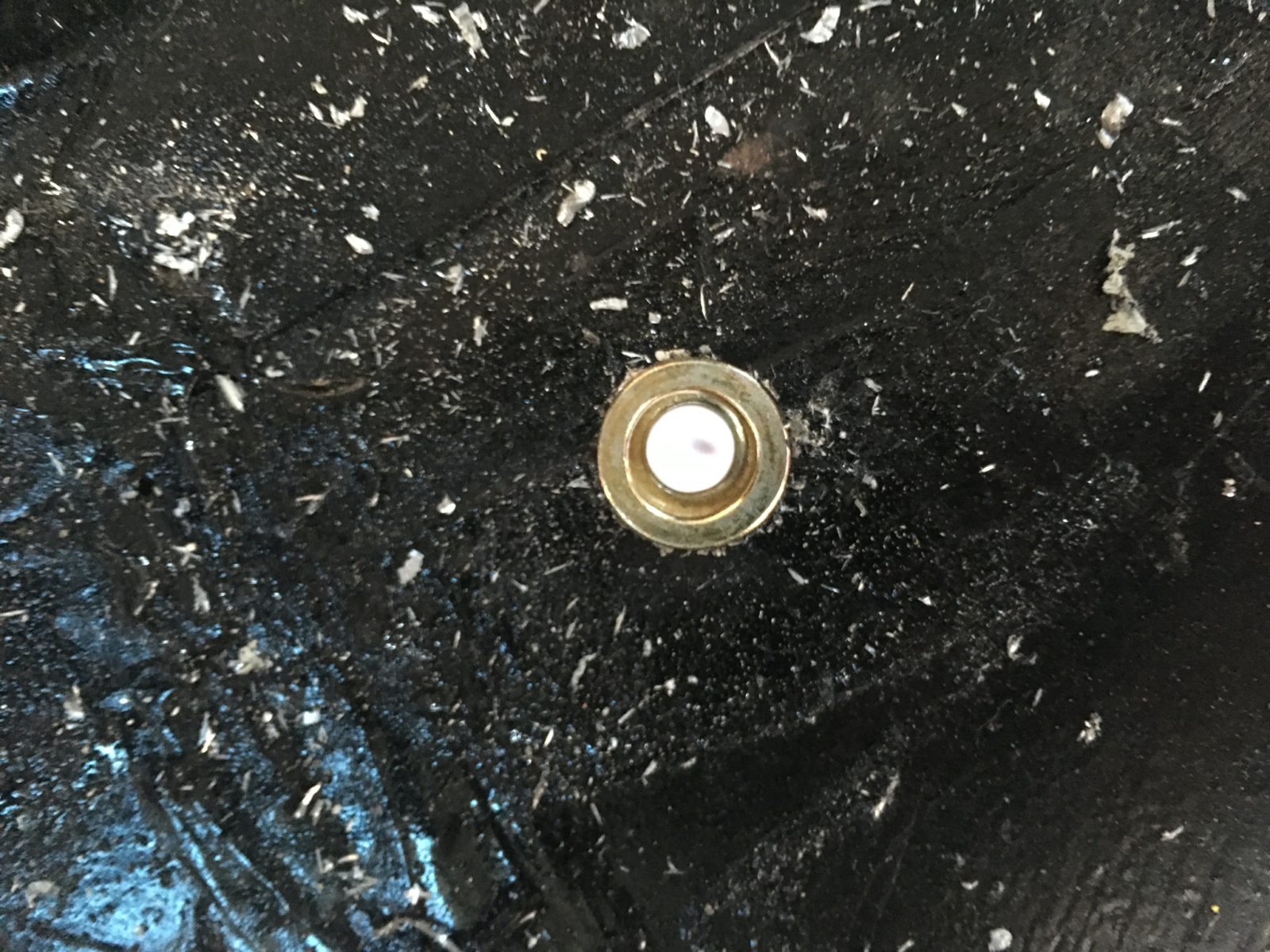
Wir behandeln als nächstes die Roststellen mit Rostschutzgrundierung (dazu bald ein eigener Beitrag) und lackieren den Boden mit einem schwarzen Karosserielack. Nun muss das Ganze gut durchtrocknen – sechs bis acht Tage sollte man warten. Achtung, der Lack ist etwas klebrig. Schmutz setzt sich leicht fest! Dafür hat er sich vielfach bewährt für Unterböden, vor allem bei Traktoren.
Im nächsten Schritt wird gedämmt: Wie bereits bei der Dämmung der Seitenwände verwenden wir Armaflex. Die 10-Millimeter-Isolierschicht lässt sich leicht verarbeiten. Man kann natürlich auch stärkeres Dämm-Material verwenden, doch wir haben das Preis-Nutzungsverhältnis abgewogen und sind daher bei 10-Millimeter Armaflex gelandet. Der Zuschnitt für den Boden ist mit Cuttermesser und Schere leicht gemacht. Die Folie wird abgezogen, das Armaflex angedrückt und schon hebt das Ganze.
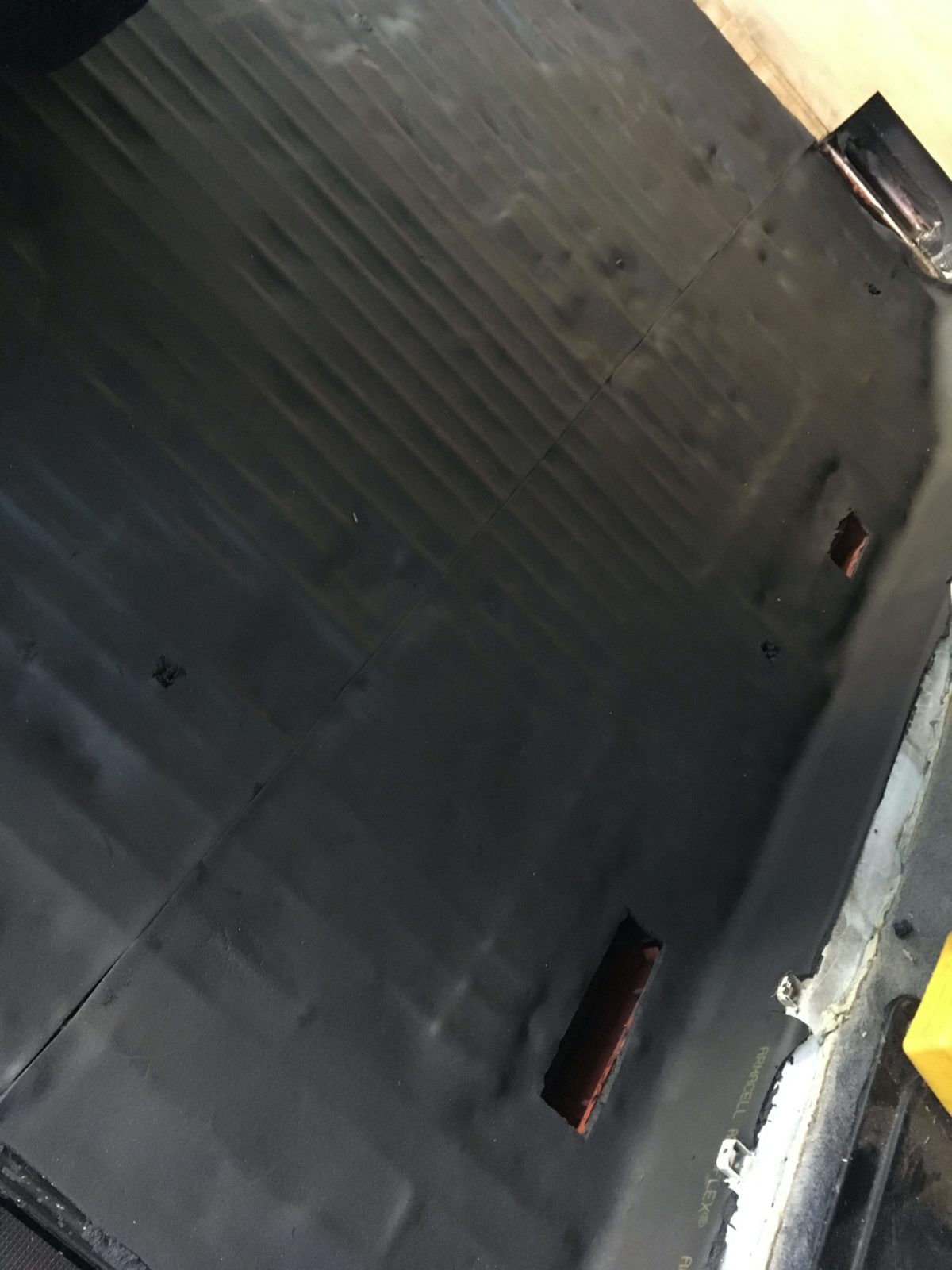
Kommen wir zur eigentlichen Bodenplatte. Wir verwenden eine Multiplexplatte. Da Ober- und Unterseite beschichtet sind, nennt man dies Siebdruckplatte. Sie halten Feuchtigkeit ganz gut aus – perfekt also für einen Camper. Alternativ lassen sich auch OSB-Platten aus verleimten und gepressten Holzspänen verwenden. Das ist günstiger, sieht unserer Meinung aber nicht so gut aus. Wichtig ist auf das Gewicht zu achten. Wir wählen daher eine Stärke von 12 Millimeter – 15 oder 18 Millimeter wären auch denkbar, sind dann aber schwerer.
Unser Tipp: Die alte Bodenplatte erst einmal behalten, um so leichter die Maße auf die neue zu übertragen. So geht der Zuschnitt viel leichter von der Hand als den kompletten Innenraum auszumessen. Alternativ kann man große Kartons nehmen und die im Wageninneren passend zuschneiden. Die dadurch entstandene Schablone nimmt man dann, um den Umriss und die entsprechenden Aussparungen auf die Holzplatte zu übertragen.
Unsere Bodenplatte ist zweigeteilt. Sie lässt sich so leichter händeln. In der vorderen Hälfte schneiden wir mit der Stichsäge die beiden Ausschnitte für die Lüftung rein. Hier kommt die Luft aus Klimaanlage und Standheizung raus. Vorgebohrt werden die Löcher zur Befestigung der Platte an der Karosserie.
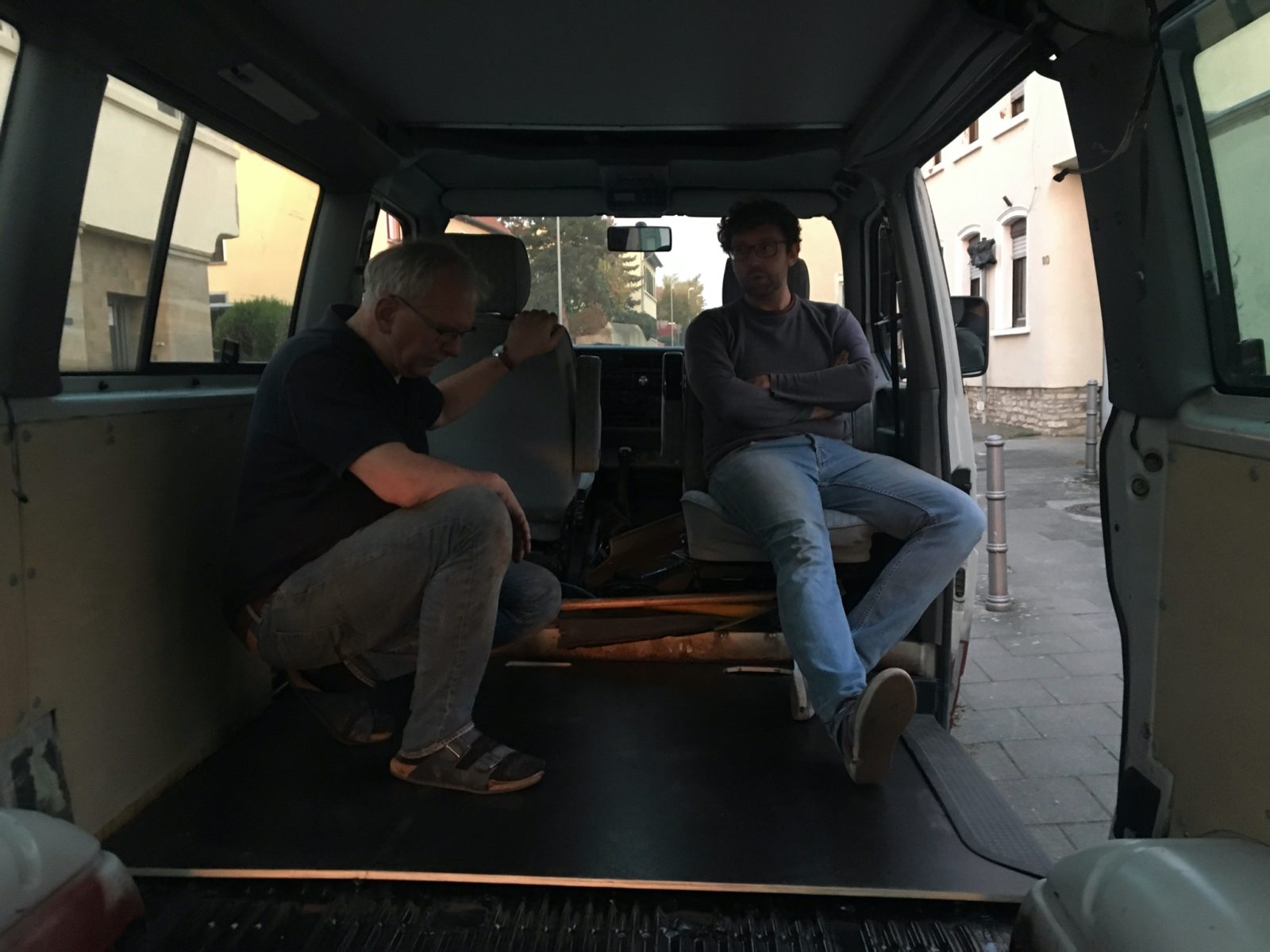
Nach dem erfolgreichen Test, ob die neuen Platten passen, befestigen wir sie. Dazu verwenden wir 8 Millimeter und 6 Millimeter Senkkopfschrauben mit Inbuskopf. Auch hier ein Tipp: Die Bodenplatten auf die Karosserie legen und die Löcher für die Schrauben von unten mit einer Spitze anreißen. Das macht man zuerst mit zwei diagonal liegenden Schrauben, die man befestigt. Er dann wird der Rest angerissen. Verwendet haben wir bei unseren zwei Siebdruckplatten jeweils neun Schrauben.
Es kann sinnvoll sein, sogenannte Gewindeplatten einzusetzen, wenn das Blech nicht das Beste ist. Die Platten überbrücken ganz gut das Wellblech am Boden und halten bestens. Es gibt sie beispielsweise bei Wiedemann Fahrzeugtechnik.
Wer schon einmal an später denken möchte: Gewindemuttern beispielsweise für die Einbauten sollten bereits jetzt mitbedacht und vorgesehen werden.
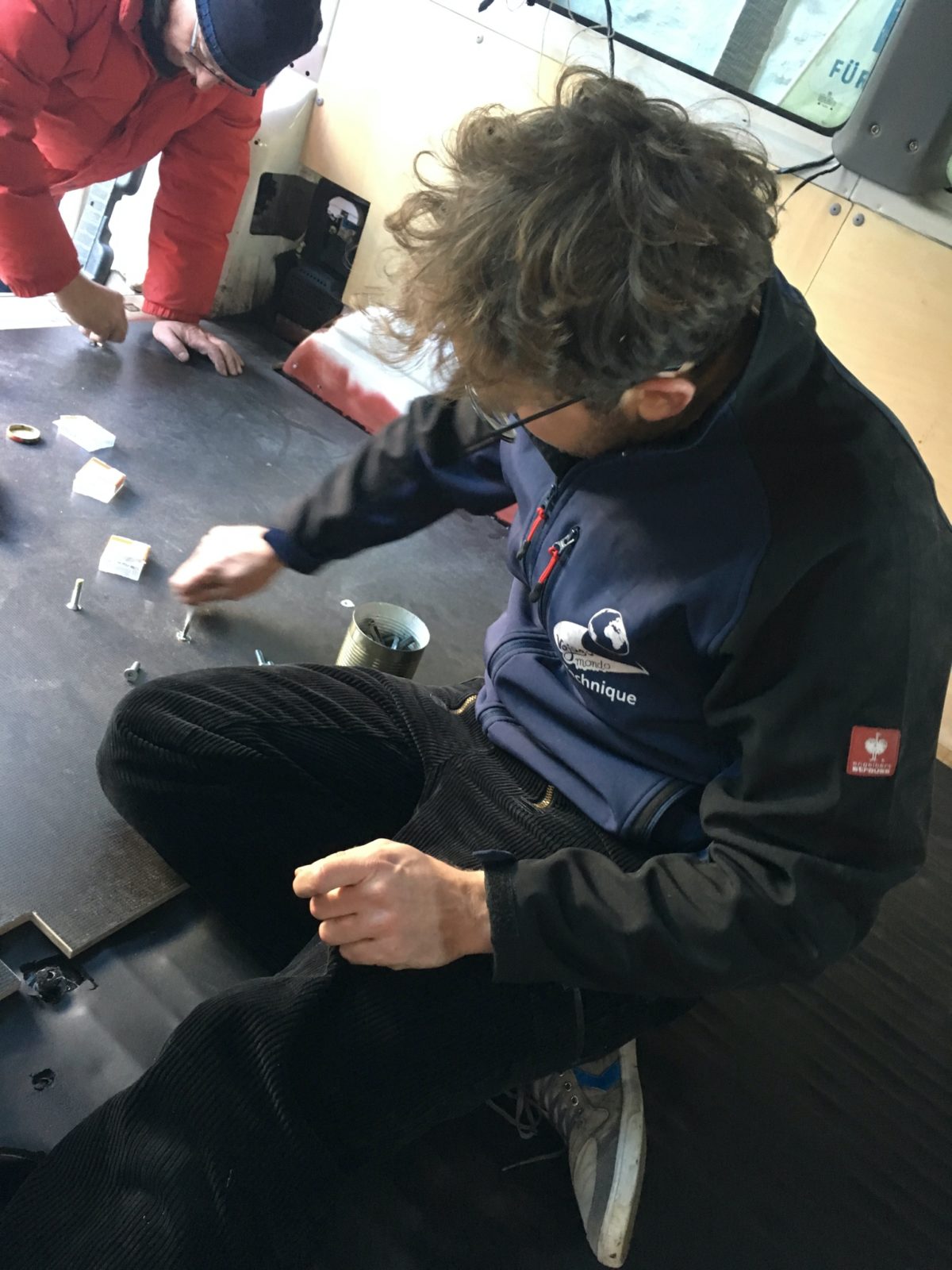
Habt ihr an den Einstieg bei der Schiebetür gedacht? Wer den Kunststoffeinstieg verwendet möchte, braucht auch hier ein Stück Platte in der gleichen Stärke wie die Bodenplatte ist. Da diese Platte keine Einbauten zu halten hat, haben wir auf Nietmuttern verzichtet und Blechschrauben verwendet.
Mit der neuen Bodenplatte sieht der Bus gleich besser aus. Und wir haben einen wichtigen Schritt beim Ausbau unseres T4 geschafft. Der wohnliche Anstrich folgt später mit der Verlegung des PVCs.
Werbung
Material:
- 12 mm Siebdruckplatten: 2 Teile für Boden, ein Streifen für Einstieg
- 10 mm Armaflex für Dämmung
- M6, M8 Senkkopfschrauben mit Inbuskopf
- M6, M8 Nietmuttern
- M6, M8 Gewindeplatten
- Blechschrauben: z.B. 3,9 mm x 25 mm, Senkkopf für Einstiegsboden
- Rostschutzgrundierung: Caramba
- Lack: Brantho Korrux 3 in 1
Werkzeuge:
- Bohrmaschine
- Nietmutternzange
- Inbusschlüssel
- Entrosten mit Winkelschleifer (Flex) mit Schruppscheibe, Fächerschleifer und Rundbürsten
- Blech raustrennen: Flex mit dünner Trennscheibe (1 mm)
- Blech schweißen mit Schutzgasschweißgerät, Draht 0,6 mm
- Spitze oder Reißnadel (Tipp: alten Schraubendreher spitz anschleifen)
- Cuttermesser
- Stichsäge
Hinweis: Einige Links sind sogenannte Affiliate Links. Das heißt, wenn ihr darüber die Produkte bestellt, erhalten wir eine kleine Provision zur Erhaltung dieses Blogs.

5 Comments
Pingback:
Pingback:
Pingback:
Pingback:
Pingback: